Concrete Repair Eau Claire is the process of repairing damaged concrete. Concrete repair steps include identifying the cause of damage, assessing the severity of the damage, selecting suitable concrete repair technique and materials, preparing for the repair process, and curing the repaired area.
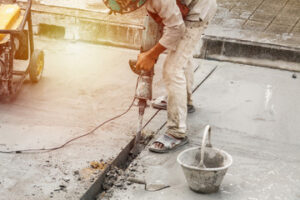
Injection methods have evolved, including products like PolyLevel that fill voids and lift concrete slabs without disturbing the surrounding soil. These products are quick, noninvasive, aesthetically pleasing and economical.
Cracks in concrete are a common problem and can lead to a range of issues that need to be addressed. Hairline cracks that are only seen from inside the home or on the surface of patios and sidewalks can be filled with DRYLOK (r) products to provide a decorative finish and prevent water penetration into the concrete causing further damage. Cracks that are visible from both indoor and outdoor spaces or are more than 1/4″ in width should be inspected by a professional and may need to be repaired using concrete resurfacing to create a new look and prevent further deterioration.
When repairing cracks in concrete it is important to understand what type of crack you are dealing with, the severity of the crack and whether or not it is active or dormant. This will help you decide which repair methods to use for the best results.
Concrete repair materials need to meet a number of properties including cracking resistance, drying shrinkage and permeability, freeze-thaw durability and bond strength. To achieve these properties a variety of construction methods must be used including proper surface preparation, wet concrete placement and curing practices.
Before repairing cracks in concrete it is important that the area around the crack is clean and free of any dirt or debris. This is crucial to ensure the repair material adheres and stays in place. This can be achieved by cleaning the crack with a pressure washer or detergent followed by scrubbing the area and roughing it up using a wire brush, stiff-bristle brush or metal scraper. It is also important to thoroughly wet the entire area before applying any repairs, this will reduce the possibility of a dry patch in the future. Once the concrete is applied it should be covered with a damp burlap sheet or plastic and taped down at the edges to keep moisture in, this will help the new repair to cure and gain strength much faster.
Delamination
Concrete is one of the most robust and long-lasting construction materials, but it’s not immune to wear and tear. One of the most common issues is delamination — a process where layers separate and cause structural damage.
Delamination is a serious problem, presenting safety hazards in heavily-traveled areas and affecting the aesthetics of concrete surfaces. It’s important to address these issues quickly to prevent further deterioration and costly repairs.
Most delaminations occur due to finishing a slab before bleed water or air has had a chance to escape, which creates “blisters” just under the surface that later break down with traffic. This is a common issue on new concrete projects.
In this case, it’s essential to ensure the mix is hydrated properly to achieve the desired consistency. The best way to do this is by using a mix design that uses ratio rather than volume for hydration. This is especially important for low slump mixes, as it helps ensure consistent, high-quality work.
It’s also a good idea to use a pre-measured system to keep track of the amount of mix used, as well as a proper mixing procedure. For example, wearing protective equipment such as respirators and gloves, add the dry mix to a bucket or wheelbarrow, then slowly pour in the water until you have reached the desired consistency. It’s a good idea to start at a 4:1 ratio (4 parts mix to 1 part water) and adjust from there, but be sure to follow the manufacturer’s instructions exactly.
Another way to help avoid delamination is by using a proper curing system. The concrete must be adequately moist cured to bond effectively with the existing concrete, reduce shrinkage and tensile stresses, and avoid excessive movement during service.
Corrosion
Traditionally, concrete repairs have involved the removal of the damaged material and replacement with new concrete or mortar. While this meets serviceability requirements, it does not necessarily meet long-term durability needs as chloride induced corrosion can continue within the repaired area.
To control this, concrete repair methods must be selected that minimize the potential for chloride penetration, promote good adhesion to the existing concrete and rebar, provide a high early strength, and resist the formation of cracks during initial curing and subsequent exposure to tensile loads. In addition, the use of corrosion inhibitors is recommended to further reduce advancing carbonation and chlorides.
The electrochemical behaviour of the steel reinforcement at the interface between the concrete patch and the surrounding parent concrete is a major concern when repairing deteriorated concrete structures, such as concrete bridges. The ring anode effect is often cited as one of the reasons for premature failure of patch repairs or increased repair volume, and is caused by the electrochemical imbalance between the steel in the patch and the rest of the structure, which results in the accelerated corrosion of the patch area (see Figure 1).
A good solution to this problem can be achieved by using a strain hardening cementitious composite (SHCC) concrete repair material. SHCC has been shown to have good flexural and restrained shrinkage properties, as well as good resistance to cracking and corrosion. Studies have also shown that, despite the fact that SHCC patch repair material is still highly sensitive to surface preparation and substrate strength, its interface tensile strength at the crack/repair zone is substantially higher than that of conventional repair materials. This enables lower stress levels and smaller crack widths in the patch.
Loose Aggregate
Aggregate is the small stones used in combination with a cementing material to form paved surfaces such as roads, driveways and parking lots. These materials are typically crushed stone such as pebbles, gravel and sand or recycled concrete. Over time, these small stones can lose their bond with the concrete and become loose on the surface of the pavement. The presence of loose aggregate is a safety concern and a liability issue. These loose stones can create a tripping hazard for vehicles and pedestrians and can dislodge paint chips from vehicle tires.
Resurfacing exposed aggregate concrete requires the use of a specialized concrete overlay or coating designed for this purpose. This can be a simple procedure if the damage or wear is limited in scope and is concentrated on specific areas of the surface. However, achieving a perfect match with the existing aggregate can be challenging.
The first step is to hose down the area of the damaged or worn concrete to remove major contaminants and loose materials. The surface should then be scrubbed using a pH-neutral cleanser that can effectively clean but also avoid damaging the exposed aggregate. This should be done carefully, since aggressive scrubbing can dislodge more loose aggregate and also impede the adhesion of repair products to the concrete.
Once the surface has been properly cleaned, the next step is to prepare the surface for a patch. Any crack, hole or dent must be repaired using a suitable bonding agent to ensure that the new patch is adhered to the concrete. In most cases, this is a slurry mix made of equal parts of sand and portland cement. Alternatively, latex emulsions with portland cement or epoxy resins can be used as bonding agents.
Damaged Reinforcement
Concrete structures are weakened by corrosion of the steel reinforcement that binds them together. When this happens, the structure becomes structurally unsound and may need to be replaced. Corrosion damage can be prevented by using the proper protective coatings or barriers, such as epoxy coatings or siloxy silicon elastomers, as well as by reversing the effects of chloride penetration by applying an anti-corrosive primer or a concrete admixture to reduce the concentration of alkali in the cement.
Concrete repair techniques can also include rebar cage welding, column jacketing and carbon wrap reinforcement systems. These techniques are suitable for repairing concrete columns, retaining walls, seawalls and other structural elements.
A common structural problem is overload damage, which can be caused by earthquakes, excessive weight placed on the concrete surface, or use of the concrete before it has reached its design strength. The best solution is to prevent structural overload by designing the concrete structure to withstand its loads and by regularly inspecting and maintaining the structure.
Another issue is freeze-thaw damage, which results from the expansion and contraction of moisture within the concrete. This can be prevented by ensuring the proper curing and hydration of the concrete, using low-alkali cement, and controlling moisture.
Other issues that can be repaired include air voids, honeycombing, streaking and dusting, which are caused by trapped air, excess moisture or temperature shifts. These issues can be prevented by ensuring the proper cure and hydration of the concrete, by adding a waterproofing sealer to the concrete and by regularly cleaning the surface to remove any dirt or debris. Preventative maintenance and regular concrete repairs will extend the lifespan of concrete surfaces and can help reduce the need for costly replacements in the future.